equipment
- Home
- equipment
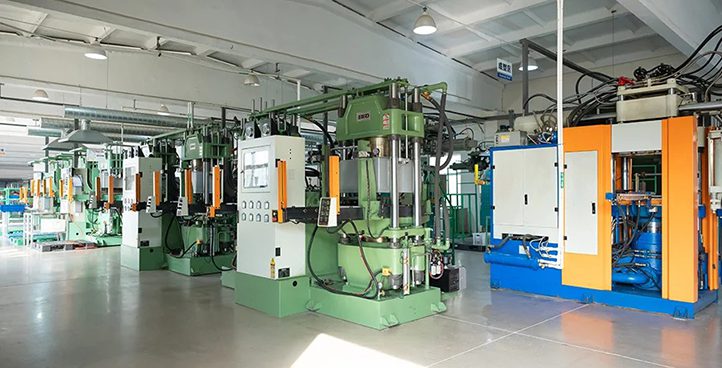
Report on the Manufacturing Capacity of Qingdao Hengjun Sealing Components Co., Ltd.
– Building a Foundation for High-End Rubber Sealing Components through Advanced Equipment
- Core Production Equipment Configuration: A Balance between Scale and Precision
Qingdao Hengjun Sealing Components Co., Ltd. relies on an international-leading rubber processing equipment system to build an intelligent production line covering the entire process from rubber material preparation, pre-forming to vulcanization and curing. This showcases its industry-leading core manufacturing strength:
- Large-scale Precision Vulcanization Equipment Cluster
– Ultra-heavy-duty Vulcanization Capacity: 700-ton flat vulcanization machine (1 unit) – Industry-leading tonnage, specializing in the precise forming of super-large and high-pressure sealing components (such as ship hatch covers, heavy machinery hydraulic sealing rings) with precise accuracy.
– 600-ton vacuum vulcanization machine (1 unit) – Specialized for high-end precision sealing components, completely eliminating bubbles and ensuring zero defects in aerospace, medical and other fields of sealing components.
– Efficient Dual-Unit System: 500-ton dual-unit vacuum vulcanization machine (1 unit) + 250-ton dual-unit vacuum vulcanization machine (2 units) + 200-ton dual-unit vacuum vulcanization machine (2 units) – **Unique “One Machine Dual Modes” configuration, efficiency increased by 40%, suitable for the production of large quantities of precision components such as automotive engine oil seals, hydraulic valve rod seals, etc.
– Flexible Production Line with Full Tonnage Coverage: 300-ton flat vulcanization machine (2 units) + 150-ton flat vulcanization machine (4 units) – Flexible adaptation for small-sized sealing components (O-rings, gaskets, shock absorbers), meeting multi-variety and small-batch customized requirements.
- Specialized Track Sealing Component Line 700-ton jaw-type track vulcanization machine (1 unit): Domestic scarce equipment, specially designed for construction machinery track sealing rings, achieving one-time forming of ultra-long dimensions (>2 meters) sealing components, overcoming industry technical bottlenecks.
– Frame-type track vulcanization machine (1 unit): Supports continuous vulcanization of complex-structured track seals, ensuring the reliability of sealing components for mining machinery and agricultural equipment in extreme conditions.
- Rubber Material Preparation and Pre-forming System
75-liter large-scale mixer (1 unit): Single batch mixing capacity industry-leading, combined with intelligent temperature control system, ensuring consistency of rubber material performance (Mentor fluctuation ≤ ±2).
16-inch mixing machines (2 units): Fine supplementary mixing and thinning to eliminate heat accumulation, improving the uniformity of rubber material dispersion.
Cold feeding pre-forming machines (2 units): Fully automatic extrusion cutting, size accuracy up to ±0.1mm, laying the foundation for efficient vulcanization.
- Manufacturing Capacity Benchmarking against Global Standards
- Scale Advantage: Total Vulcanization Pressure exceeds 3100 tons: 60% of equipment is over 300 tons, possessing monopolistic manufacturing capabilities for heavy/ultra-heavy sealing components.
– Vacuum Vulcanization: 45% – Vacuum equipment covers the core range of 250-600 tons, with the quality rate of high-end products exceeding 99.2%.
- Technical Depth: The only enterprise with both 700-ton jaw-type track machine and frame-type track machine, monopolizing the domestic market for construction machinery track sealing.
Dual-unit system enables “large-scale production of precision sealing components”, with a daily production capacity of 200,000 pieces (based on standard O-rings).
- Lean Manufacturing
Closed-loop control throughout the production process from mixing to pre-forming to vulcanization, product traceability rate reaches 100%.
Equipment automation rate 85%, reducing size fluctuations caused by human intervention.
III. Empowering High-End Application Fields
With a complete equipment matrix, Hengjun Sealing Components can provide **full-scenario sealing solutions for harsh conditions:
– Heavy Machinery**: 700-ton vulcanization machine ensures one-time forming of the main drive sealing ring for shield tunneling machines (diameter > 1.5 meters)
– New Energy Vehicles**: Vacuum vulcanization units produce hydrogen fuel cell bipolar plate sealing components (pressure ≥ 5 Bar)
– Special Equipment**: Track line dedicated to manufacturing armor vehicle load-bearing wheel sealing rings (resistant to sand impact for 2,000 hours) – Medical Equipment: 150-ton precision vulcanizing machines produce dialysis equipment sealing valves (biocompatibility certification)
Qingdao Hengjun Sealing Parts Co., Ltd. uses a cluster of equipment featuring **heavy-duty, vacuumization, and specialization** to redefine the manufacturing standards for rubber sealing parts: Scale barrier: The largest concentration area of tonnage vulcanizing equipment in North China. Technical barrier: Vacuum vulcanization + dual-unit efficiency + track-specific line integration. Quality barrier: Full-link precision guarantee from rubber dispersion to vulcanization micro-control. With a steel body, we forge the soul of sealing – Every piece of equipment in Hengjun Manufacturing Base is the ultimate endorsement of the reliability of high-end sealing parts.
Qingdao Hengjun Sealing Parts Co., Ltd.
Address: Daxin Street, New Economic Development Zone, Qingdao City, Shandong Province
Telephone: 18953206626, WhatsApp: 18653206626 http:www.globalrubbersealing.com
The leader in full-scenario solutions for sealing systems